Effect of the Depth of Cut on the Age of High-Speed Steel (HSS) Lathe Tool for the Low Carbon Steel Outer Turning
Keywords:
Low carbon steel;, deep of cut, feed, wear edgeAbstract
Abstract
In the machining process, there are three parameters that need to be determined before the machining process is carried out, namely: depth of cut (a), feed motion (f) and cutting speed (v). Determination of the three parameters of the machining process will determine the quality of the product to match the desired geometry and tolerance. The three parameters of the machining process will affect tool life, where the selection of a constant depth of cut and feed motion will produce the most optimum level of tool wear. This study used several machining parameters with several variations, namely: depth of cut (a) of 0.5 mm; 0.8mm; 1.1mm; and 1.4 mm and feeding motion (f) of 0.062 mm/revolution and 0.1 mm/revolution. The machining process is carried out at a constant (n) rotation of 425 rpm. Based on the research that has been done, it was found that the tool life on the feed motion (f) = 0.062 mm/revolution is better than that on the feed motion (f) = 0.1 mm/revolution, where at (f) = 0.1 mm/revolution chisel wears out faster. Optimum cutting conditions are produced at feed motion (f) = 0.062 mm/revolution and with a depth of cut (a) = 1.1 mm where the production cost (Cp) is Rp.746.56/product.
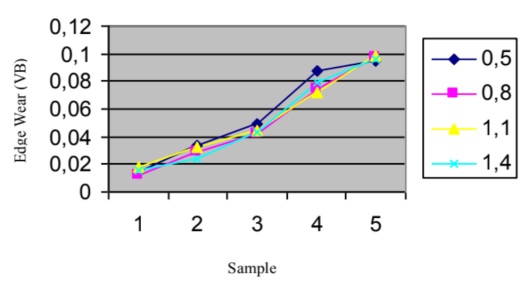